Sand casting is an ancient art form that has been used for centuries to shape and craft a variety of items from metal, glass, and ceramic. Despite its long history, the science behind sand casting remains largely unknown to many modern-day craftsmen.
This article seeks to provide an overview of the art and science involved in sand casting, exploring topics such as types of molds used, material selection criteria, processes, and techniques for creating a successful cast product. It will also discuss various applications where metal casting can be utilized such as automotive components or sculptures. By understanding the complexities involved in this method of forming products from molten material, readers will gain insight into how they can apply their knowledge in different settings.
Understanding the Basics of Sand Casting
Sand casting is a centuries-old art form that has been used for creating everything from tools to decorative objects. In essence, sand casting involves pouring molten metal into a mold made of sand and allowing it to cool and harden.
This process requires an understanding of how different types of molds can affect the outcome; careful preparation and execution are essential for successful results. Additionally, various techniques have been developed over time to further refine the craftsmanship involved in sand casting.
At its core, sand casting involves making a cavity or negative impression in a refractory material (usually dry or dampened fine-grained sand) known as “the mold” which will contain the molten metal once poured inside. The mold is created using either hand-carving tools such as chisels or other specialized equipment like diecast machines.
Depending on what type of object is being crafted, additional steps may be necessary before pouring begins – these might include reinforcing cavities with cores and shaping external surfaces with parting agents respectively called ‘cope & drag’ operations. After this step is completed any excess material must be removed by filing or grinding before cooling takes place for the finished product to meet desired specifications.
Finally, post-casting treatments such as heat treatment can also add strength and durability while increasing aesthetic value when applicable (e.g.
, adding color). All these variables make sand casting an intricate yet rewarding activity – one that requires both patience and skill but ultimately yields beautiful pieces that reflect their creator’s passion for craftsmanship!
Materials Used in Sand Casting Processes

The materials used in sand casting processes can have a major impact on the quality and success of the finished product. Sand casting entails pouring molten metal into a mold made from sand, which is held together by a binder.
The type of material used for both the sand and binder will affect how well the cast works, as well as its strength and durability. Commonly used materials for sand casting include silica sands, olivine sands, chromite sands, zircon sands, alumina-based refractory sands, and calcined fire clays. Each type of material offers unique properties that make it suitable for certain applications or specific project requirements.
Additionally, other elements such as resins may be added to ensure that molds hold up against high temperatures during casting procedures. With a careful selection of materials to suit individual needs, sand casting can produce strong and reliable parts with excellent surface finishes that are ideal for many industrial purposes.
Finishing Techniques for Achieving Desired Results
When sand casting, the finishing techniques used to achieve the desired results are just as important as the process itself. Finishing and post-production processes can include grinding, shot blasting, fettling, heat treatment, and polishing.
These different steps allow for a more precise finished product with improved surface finish and dimensional accuracy. Grinding helps remove imperfections created during the casting process while also shaving off excess material from cores, risers, or other areas of the cast part.
Shot blasting is used to create an even texture on the surface of a metal by applying small particles of media at high velocity which clean away any residual dirt or debris that was missed during cleaning operations. Fettling involves the manual trimming of gates and sprues along with minor repairs such as patching porosity flaws or filling in gaps between two sections of a cast part.
Heat treatment is sometimes necessary depending on what type of metal was used for casting but primarily it’s done to increase strength properties like hardness while reducing brittleness in some cases. Finally, polishing gives parts their final gloss finish before they’re ready for use in whatever application they were made for originally.
Conclusion
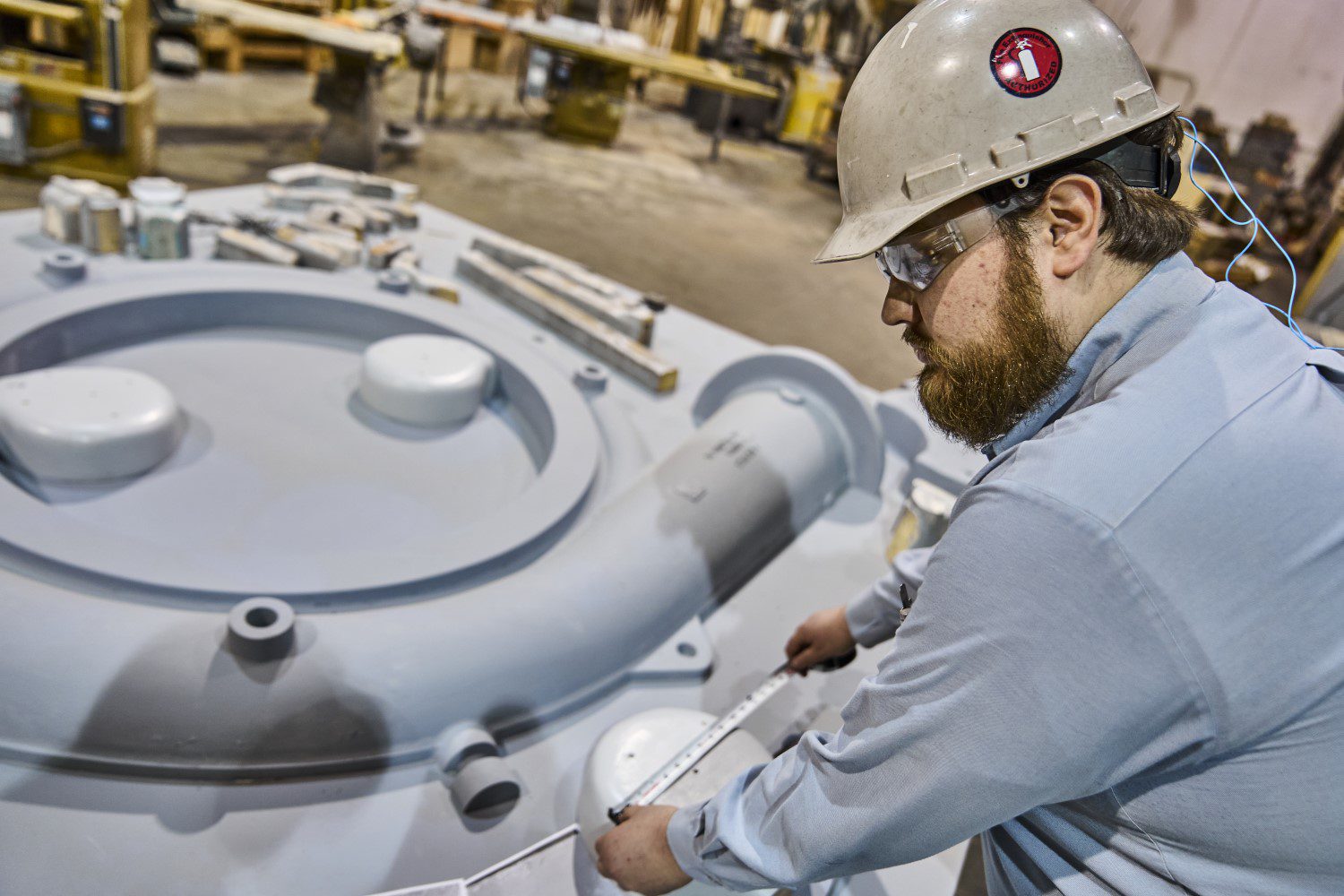
Sand Casting is an ancient art and science that dates back thousands of years. It is a process in which molten metal is poured into a mold, often made from sand, allowing it to cool and take shape. Sand casting has been used in many industries for centuries due to its versatility and durability when compared to other manufacturing processes.
In modern times, advances in technology have enabled manufacturers to create complex shapes with greater precision than ever before. The combination of traditional techniques with modern innovation allows for the creation of intricate parts at low cost while maintaining high standards of quality control.